What the Solar Panel Manufacturing Process Actually Looks Like
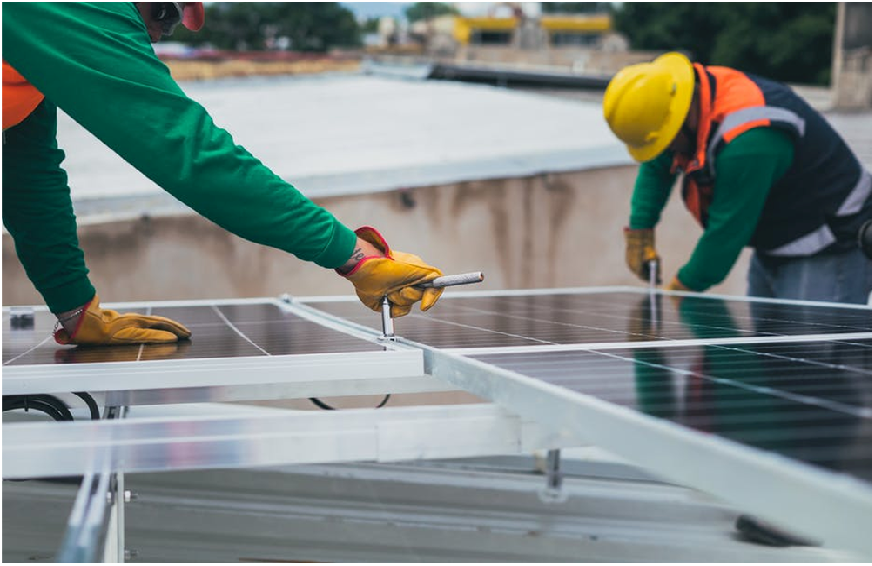
The solar industry continues to explode in the US market. Every year, more and more households are switching over to solar energy in whole or in part. Just in the last decade, solar energy experienced a 42% average annual growth rate.
Major federal policies and declining costs of materials have contributed to the expansion of this innovative technology. Estimates suggest that there is more than 100 GW of solar energy nationwide.
This begs the question of how solar panel manufacturing really works. Where do companies source material to create panels for residential solar installations?
In this article, we will walk you through everything you need to know about solar industry manufacturing and how to find the best solar company as a smart homeowner who wants to invest in their future.
Solar Panel Manufacturing: An Overview
When driving past a home with solar installed on the roof, you probably envision several large panels placed together in series. You’re looking at the final product of a lot of hard work created by many hands.
These black solar panels employ some extremely complex technology. They used silicon semiconductors to help absorb the energy from sunlight and turn it into an electric current.
The panels include numerous solar photovoltaic cells built in series together. The cells contain several silicon layers that help to provide additional electrons that can move around be one of two types of semiconductors. They can be positive or negative silicon layers.
When solar energy strikes the panel, negative silicon layers disperse an excess of electrons throughout the cell. On the other hand, the positive type layer has areas where electrons can move to two fill in vacancies. The industry calls these holes.
Placing these two types of layers in series allows for a mechanism of flow of electrons once electrons have dispersed by light energy striking the panel.
As soon as sunlight hits the junction between the two, a special photon from the sun can push an electron from the negative type layer to the positive type layer. Eventually, the resulting current collects at the pole of the cell.
Once electrons have reached the pole, a form of direct current exists. An inverter turns this direct current into an alternating current the conventional form of electricity that most home appliances use via a wall socket. The alternating current will go to the breaker box or central panel for appropriate distribution to the electrical system based on current needs.
So, how is all of this built?
Some Background on Solar Panel Manufacturing
The story of modern solar systems starts in 1954. During this time, Bell Labs produced the first photovoltaic cell that relied purely on solar energy. This invention had been in the works for many years.
Bell Labs played around with different materials to try to find something that would allow for good efficiency at the positive to negative layer junction.
They found that silicon fit the bill. The good news for the company was that silicon is a very abundant material in the Earth’s crust.
Bell Labs decided to employ the special properties of silicon as a semiconductor by building it into a series of photovoltaic cells. This created the first modern solar cell.
Modern Manufacturing
Several other manufacturing processes go into creating a full-scale solar panel system.
First of all, modern photovoltaic cells are usually mass-produced in a factory using special silicon cut by lasers. This is very different from the original solar cells produced by Bell Labs.
As mentioned, there needs to be an inverter to help convert the electricity into a usable form. This can be manufactured by the company directly, or outsourced to a third party that specializes in inverters.
Lastly, the cells need to take a system that can be attached to a roof or surface. Once again, this can be outsourced or can be developed in-house for improved efficiencies.
Most companies will choose to do everything on their own to ensure the highest power output in the final product. Mounts usually come in 30 or 45° angles, which is determined by the distance of the panel from the Earth’s equator.
Fixed amounts keep the solar cells fixed throughout the day. However, more complex track amounts can essentially follow the sun to improve efficiency as it travels across the sky hour by hour.
The Streamlined Process
Today, the way all this works starts with taking pure silicon or combining multiple silicon fragments and melting them into a singular piece. Once the primary silicon piece forms, the cell goes into a special mold creating a cell.
Many cells combine together in series using soldering techniques. Usually, there are 60 or 72 cells in a crystalline panel.
After these cells have been combined together a back sheet installs onto the bottom of the cells. In most cases, a glass front installs over the top while also providing additional protection.
Then, a metal frame is placed all the way around the panel that fuses all of the layers into one major piece.
A junction box is installed onto the electrical wires to prevent damage. This reduces the need for ongoing maintenance. After this, everything is in place, and the solar panel is ready for use.
Keeping up With Manufacturing Practices Today
At the end of the day, the overall process for solar panel manufacturing is relatively standard across manufacturers in the industry. The greatest challenge comes from sourcing and molding silicon to increase overall efficiency. From there, back sheets and a protective glass layer are placed onto the cells with a metal frame that creates a panel ready to be shipped out.
If you enjoyed this article about professional solar production, please check out our other articles on future kids.org!